PUPPET MASTERS
How 3D printing helped create the Oscar-nominated Guillermo del Toro's Pinocchio's main character.
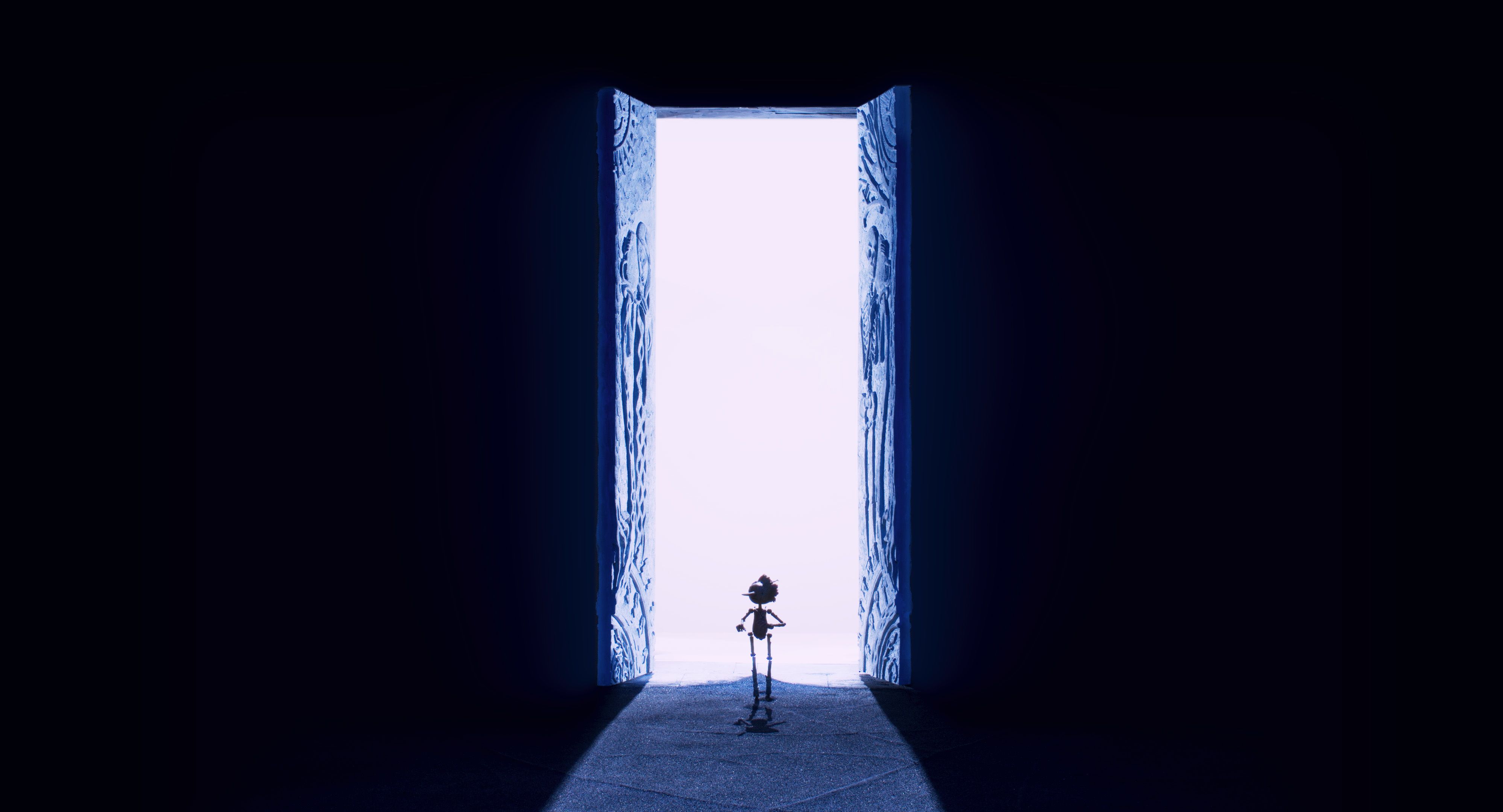
“A story about puppets, acted by puppets. You don’t have to believe they are real people – you have to believe in them as characters.”
These words, posted on the Mackinnon & Saunders Instagram page in January 2023, only fell out of Guillermo del Toro's mouth on the promo trail ahead of the release of the Oscar-winning director's Pinocchio movie late last year, but it serves as both the organisation's brief for the project and the reason it does what it does.
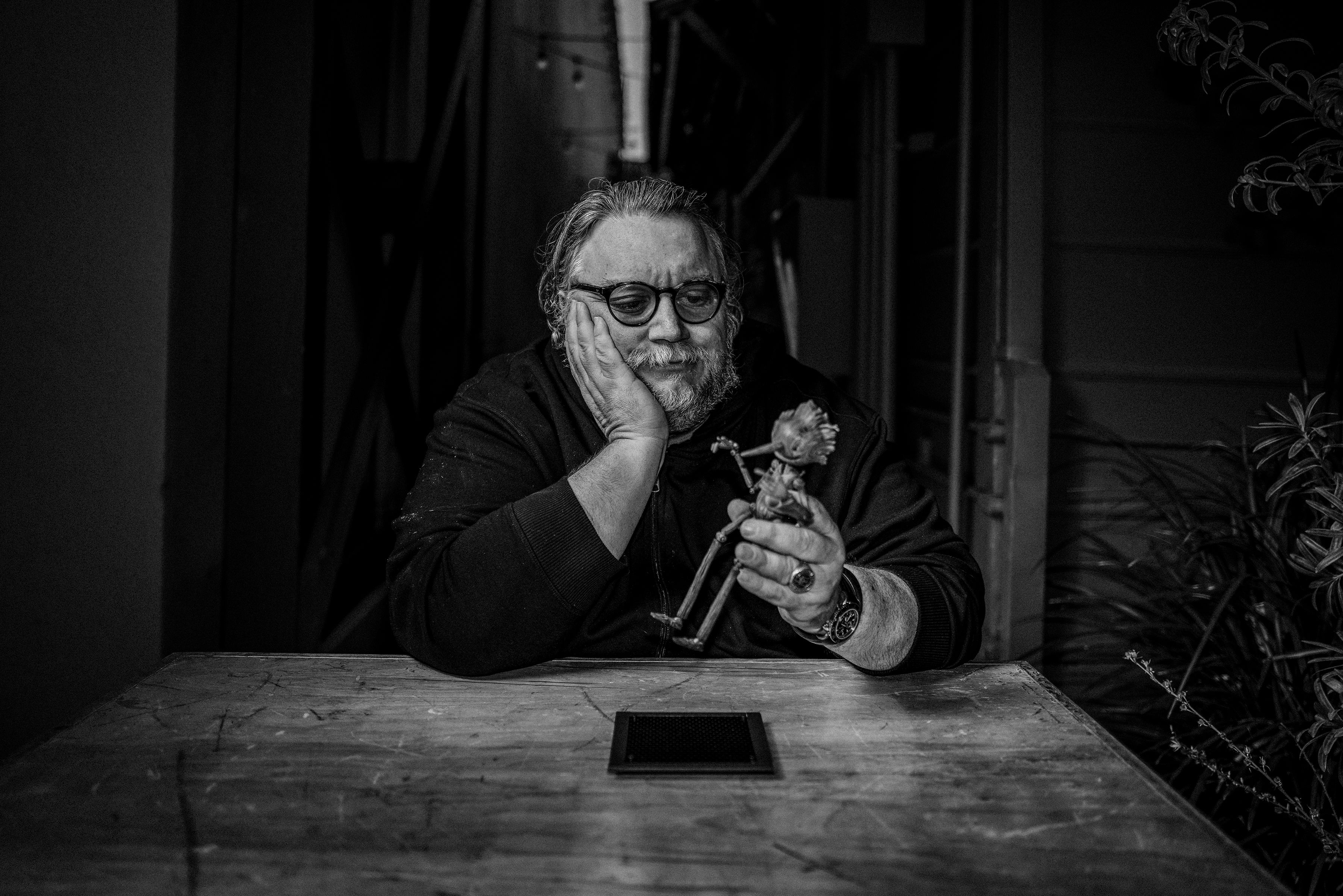
Based in Manchester, UK, Mackinnon & Saunders is renowned for its puppet-making prowess. But over its 30-year lifespan, it has had to overcome a scepticism for the longevity of stop motion.
At the turn of the century, advancements in computer-generated imagery (CGI) threatened to diminish its popularity. But two decades on, Mackinnon & Saunders’ role in the making of a certified box office hit that has won Best Animated Feature at the Golden Globes and received a nomination in the same category at the Academy Awards speaks for itself.
Not only has CGI progressed, but so too have the techniques behind stop-motion animation films like Pinocchio. Indeed, the same Instagram post that referenced del Toro’s pointed assessment of stop motion also eulogised about the ‘first stop motion puppet to be animated in a major movie with an armature created almost entirely with metal 3D printing technology.’
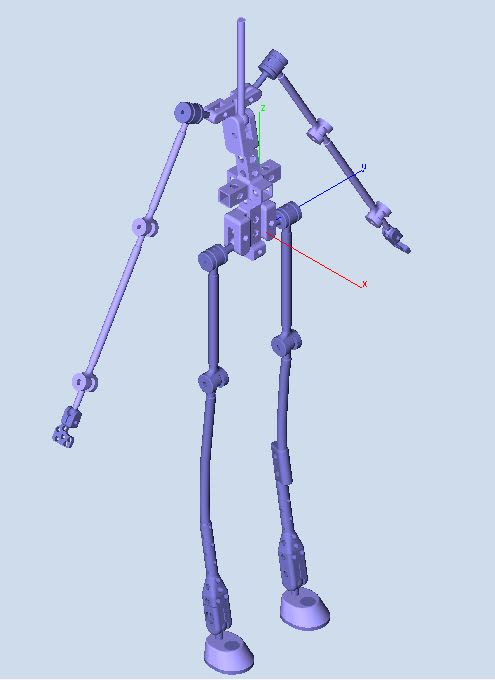
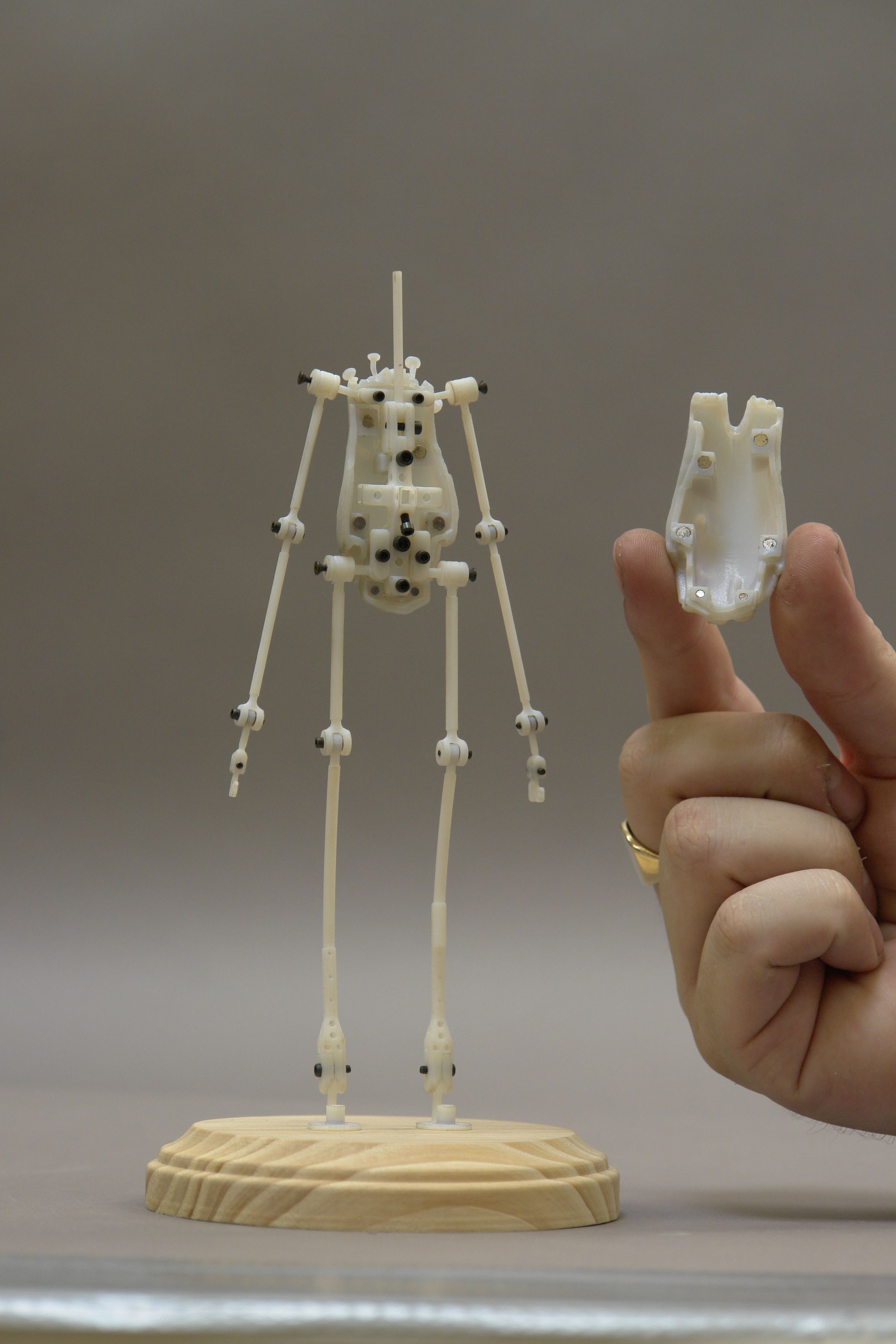
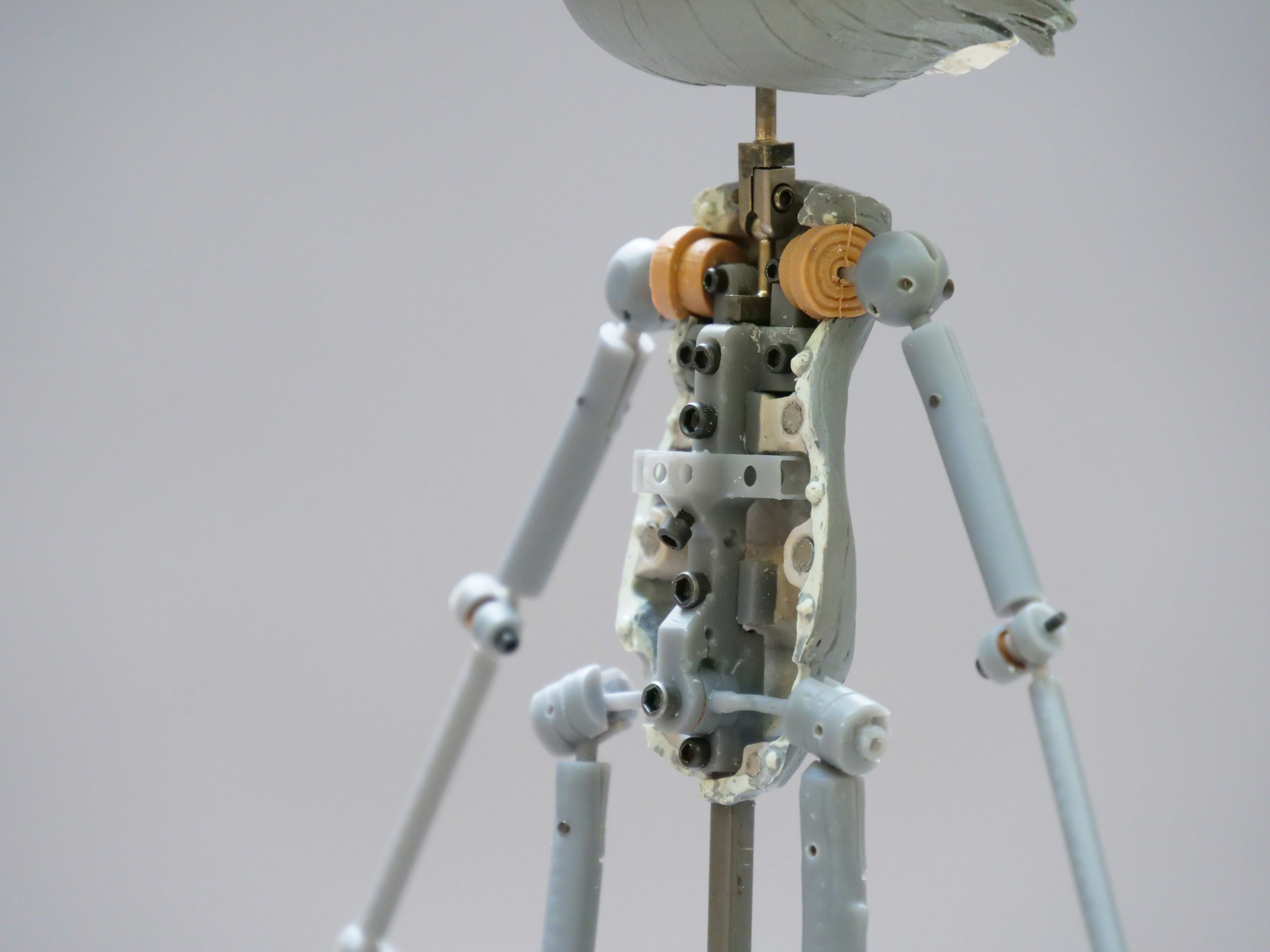
"With traditional techniques, we'd struggle."
Guillermo del Toro was holding conversations with the likes of Mackinnon and Saunders as early as 2008, 15 years before the movie’s release, 10 years before Netflix would commit to the work, and even before the Manchester-based firm had started to utilise 3D printing.
“If we’d tackled the film 15 years ago, we wouldn’t be able to do half of what we can do now,” co-founder Ian Mackinnon tells TCT.
“It would have been a different film,” Richard Pickersgill, Workshop Supervisor & Puppet Maker, agrees. “All the characters would have been designed differently.”
While del Toro chased a career-long dream, discussions commenced on how to bring Pinocchio to life – in a more sophisticated way than the drunken Geppetto manages in the movie, but with the same heart.
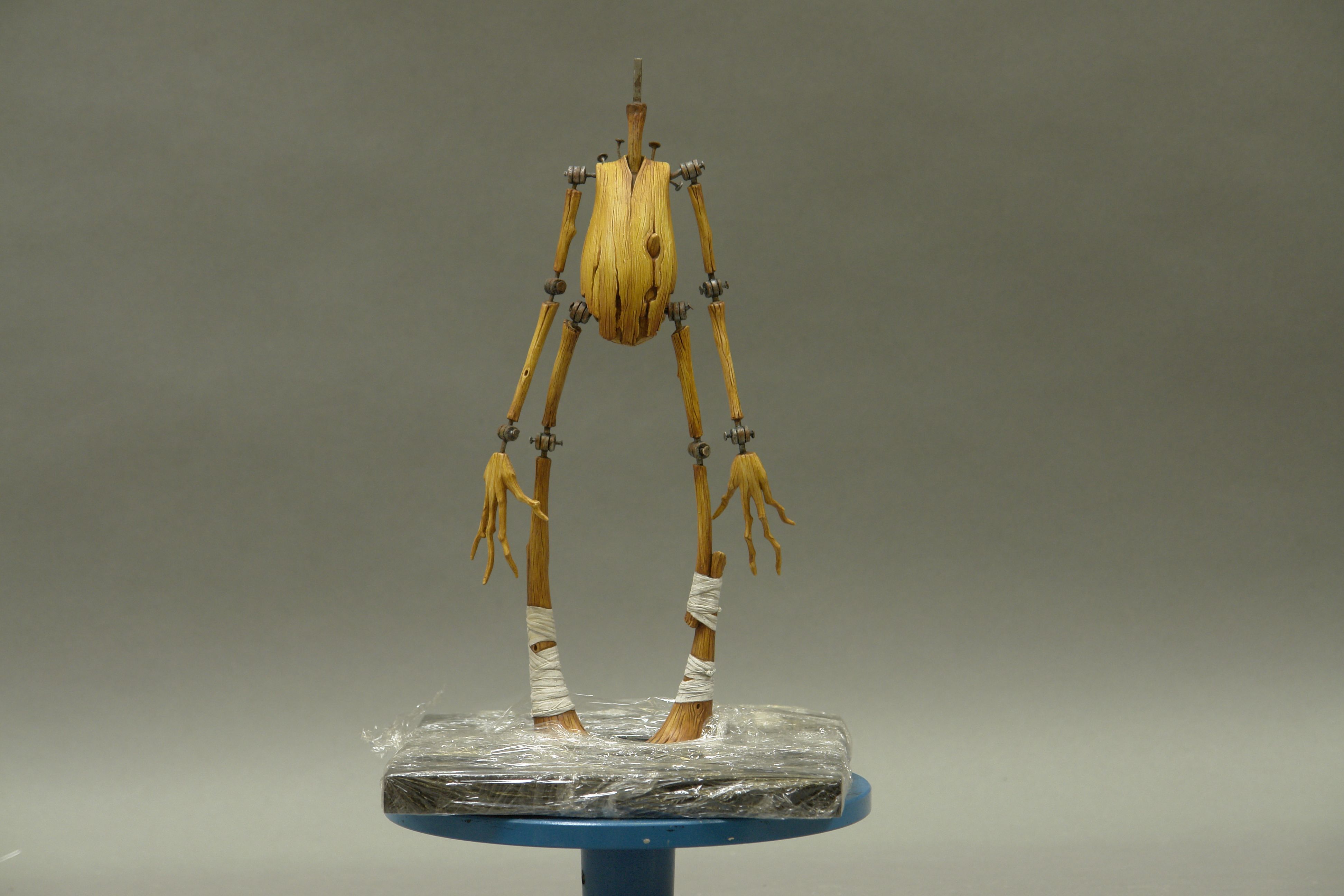
Once the design brief had been outlined and the scales of characters and sets aligned, Mackinnon & Saunders knew they were looking at the creation of a small puppet with extremely thin limbs. This presented a challenge.
“As much as possible, we want to maintain that vision of the director,” Pickersgill says, “so, we knew quite early on with Pinocchio that, with traditional techniques, we’d struggle to create a strong enough puppet to withstand two years of animation. [Traditionally], you would make the armature and the skeleton underneath and then cast parts over it. If we did that at the scale Pinocchio was at, it would have unlikely been able to self-support and hold its own weight. So, it would mean it would have to be rigged, and that would have added cost, time, and post-production.”
While design deliberation continued, a maquette form of the Pinocchio puppet was worked up in plasticine over a wire framework. At this early stage, Pickersgill would also often lean on in-house Formlabs Form 2 machines to prototype the puppet’s armature. As designers, directors and puppet-makers went back and forth, the decision was made to separate the head, separate the arms, and deconstruct the hands. In other instances, there might have been scope to produce a mould and put an armature inside to build the puppet, but for Pinocchio, a predominantly 3D printed armature was the way to go.
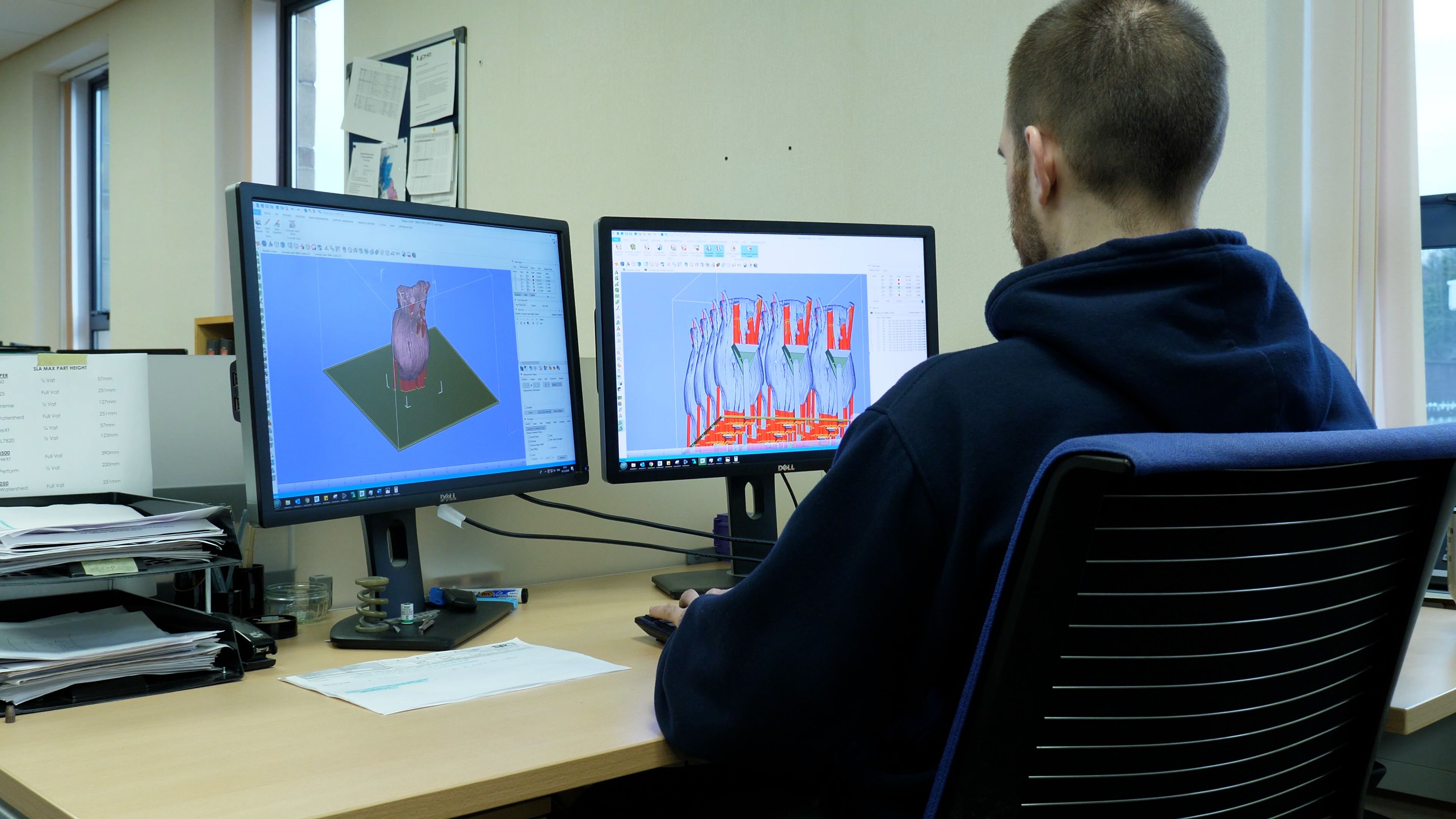
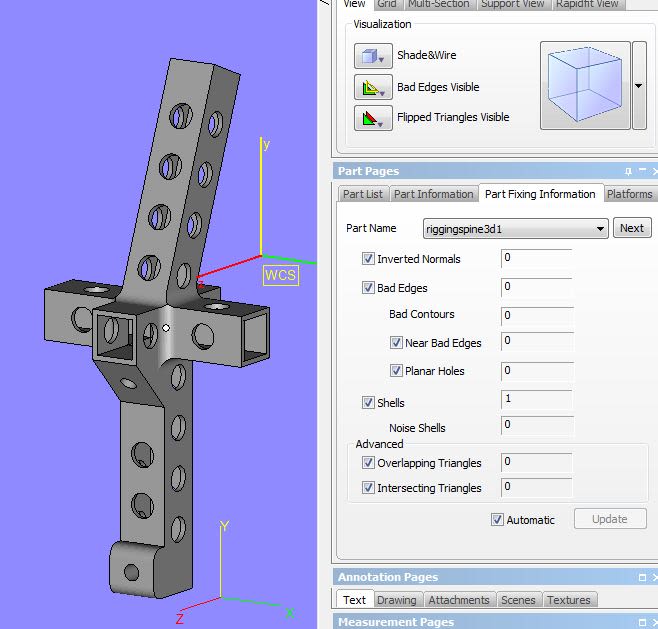
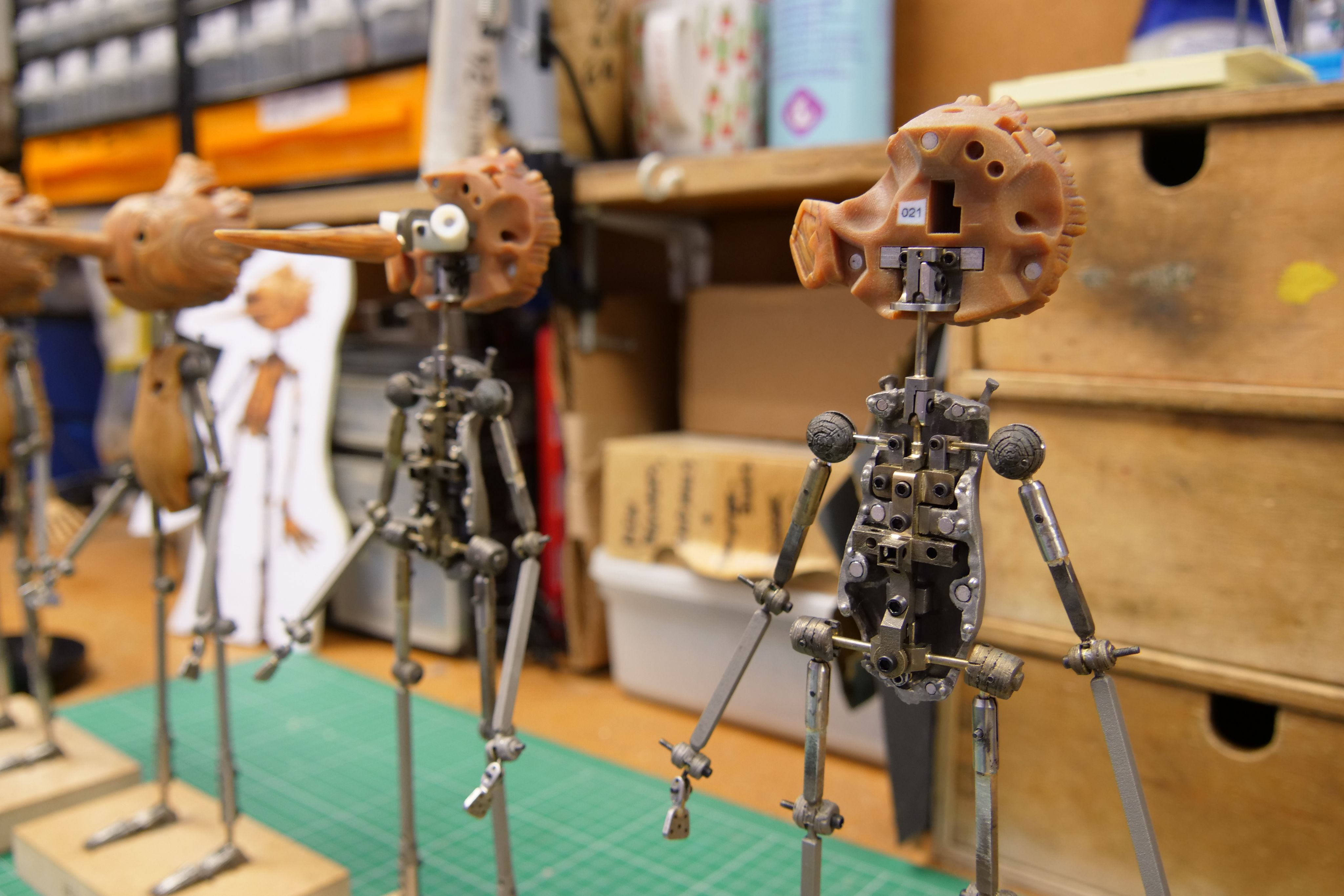
"3D metal printing allowed us to make a puppet that was much stronger."
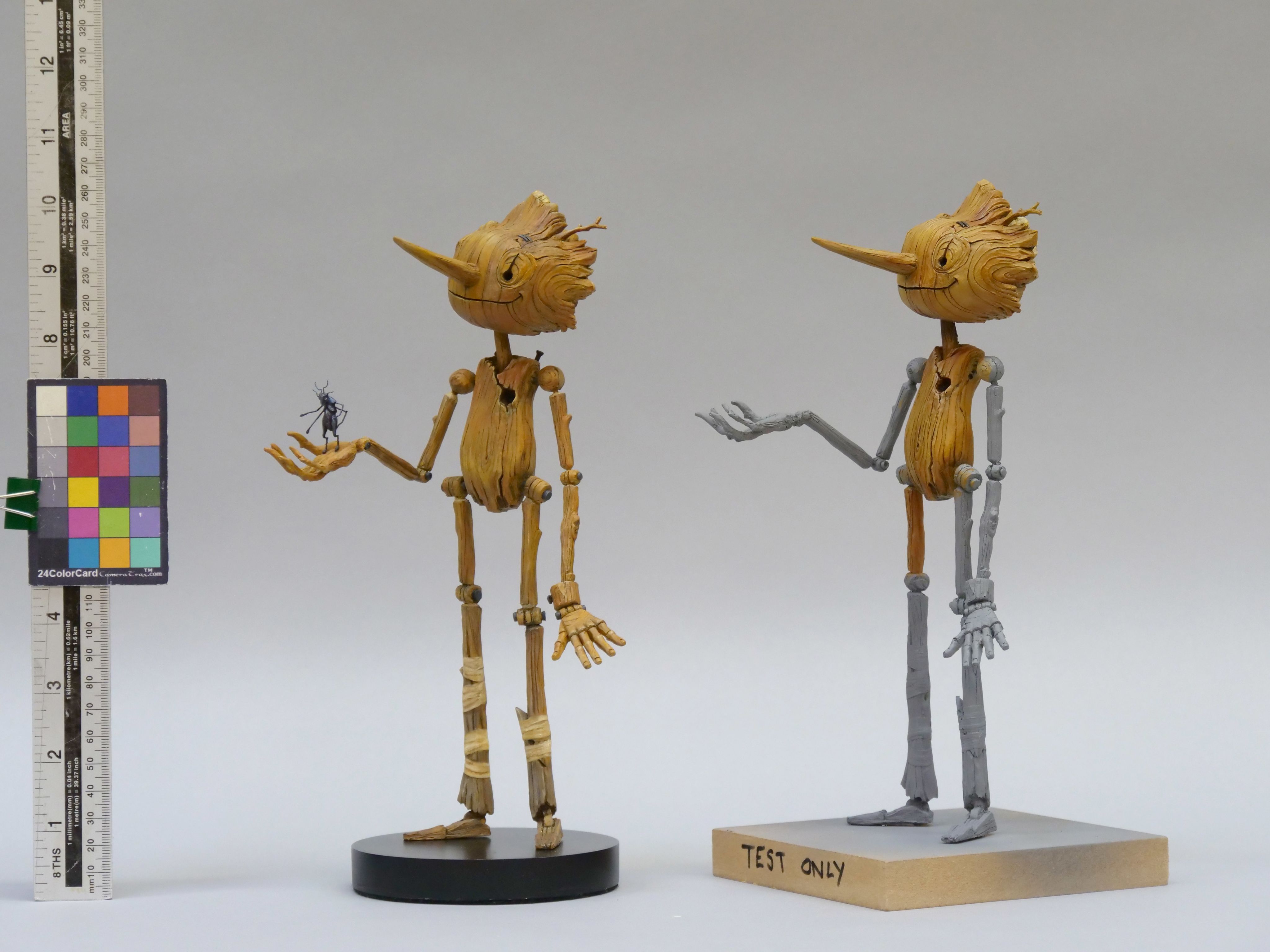
Made up of more than 100 components and hinges, metal 3D printing was leveraged for the main spine, rear torso shell, hip clamps, hip joints, feet, ankle clamps, lower legs, knees, thighs, lower arms, upper arms, and shoulder clamps.
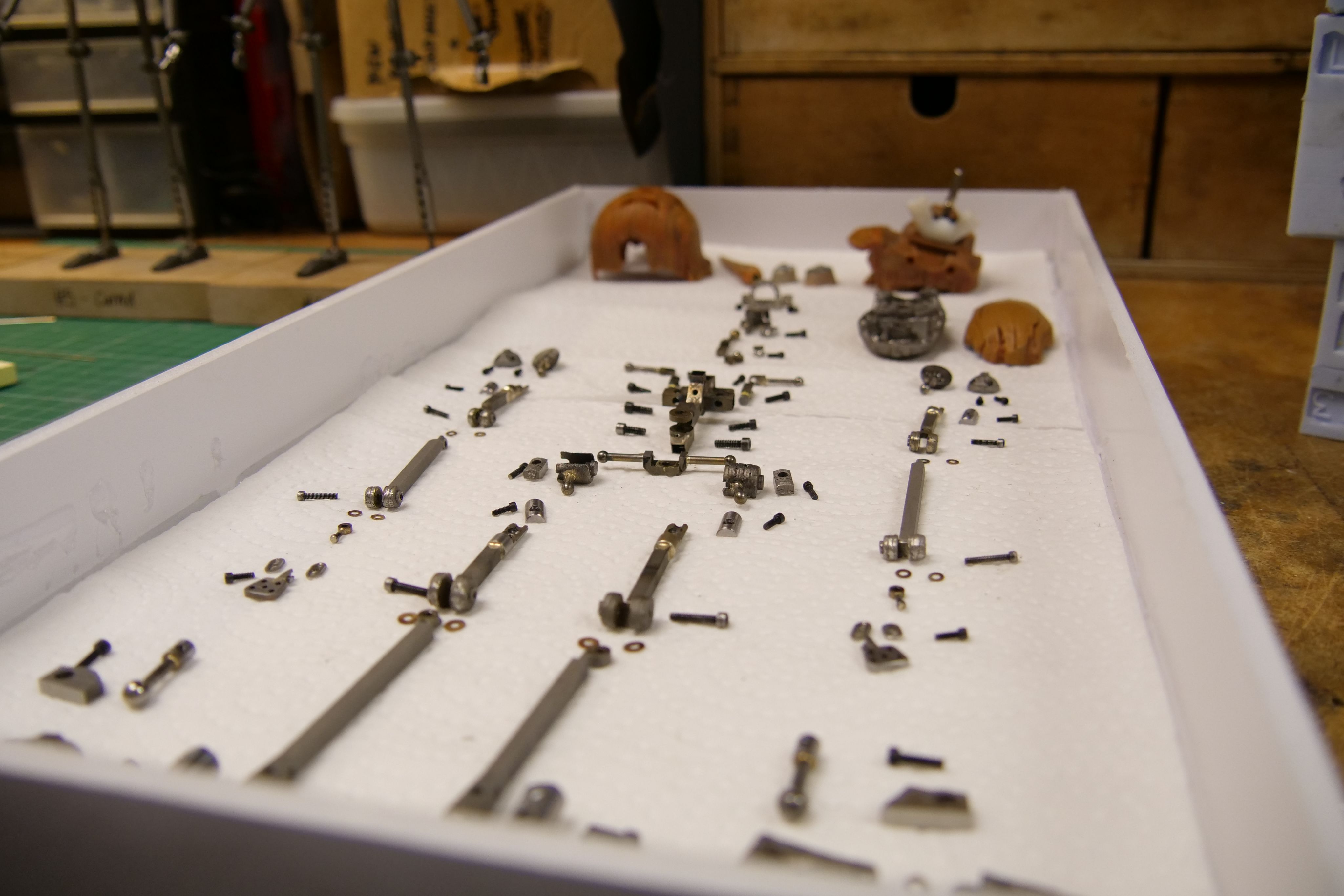
Belfast service bureau LPE was called upon to harness its Concept Laser MLab capabilities to prototype the armature components in stainless steel. Smaller armature parts were printed in builds of around four hours, while the rear torso shell took up to 30 hours. This part, the most challenging per LPE, required some in-house R&D to create custom supports to keep the support material from colliding with the wood effect surface. To ensure consistency, the same team member would be in charge of printing the same components. A team of five were then responsible for finishing the parts, with holes and linkages needing to be as precise as possible to enable optimal movement – some printed holes were as fine as 1mm.
Meanwhile, the head and external torso elements of the plasticine sculpt were 3D scanned, with the data being used to model parts that would then be printed in full colour with a Stratasys J750 by manufacturing bureau FATHOM. With this data uploaded to a CAD platform, the torso shell was hollowed out to allow the inner technical workings to be placed, and a split was implemented across the head to allow the mask to come away from the back of the head as a replacement, enabling different facial expressions to be shot without too much clean up required in post-production. FATHOM ended up producing thousands of iterations of the face, its features, and the torso. Using digital sculpting and painting software, the company provided requirements for the translation of a digital sculpture into a 3D printable object with texture mapping to accurately represent the intended shape and colours. For quality control, FATHOM calibrated and validated the driver settings of a single machine and took steps to control material batches, while a lighting rig was installed to measure prints against the ‘gold standard’ set out by the animation team.
Despite all that, Pinocchio’s dishonesty would still cause challenges.
“The branch noses were incredibly challenging, because you have to clean them and rinse off the support structures,” FATHOM CCO Rich Stump notes. “You can’t have any chips, damage, or warping. As [the] nose grew, that became more of a challenge because it can be more delicate. These challenges, you have to design around.”

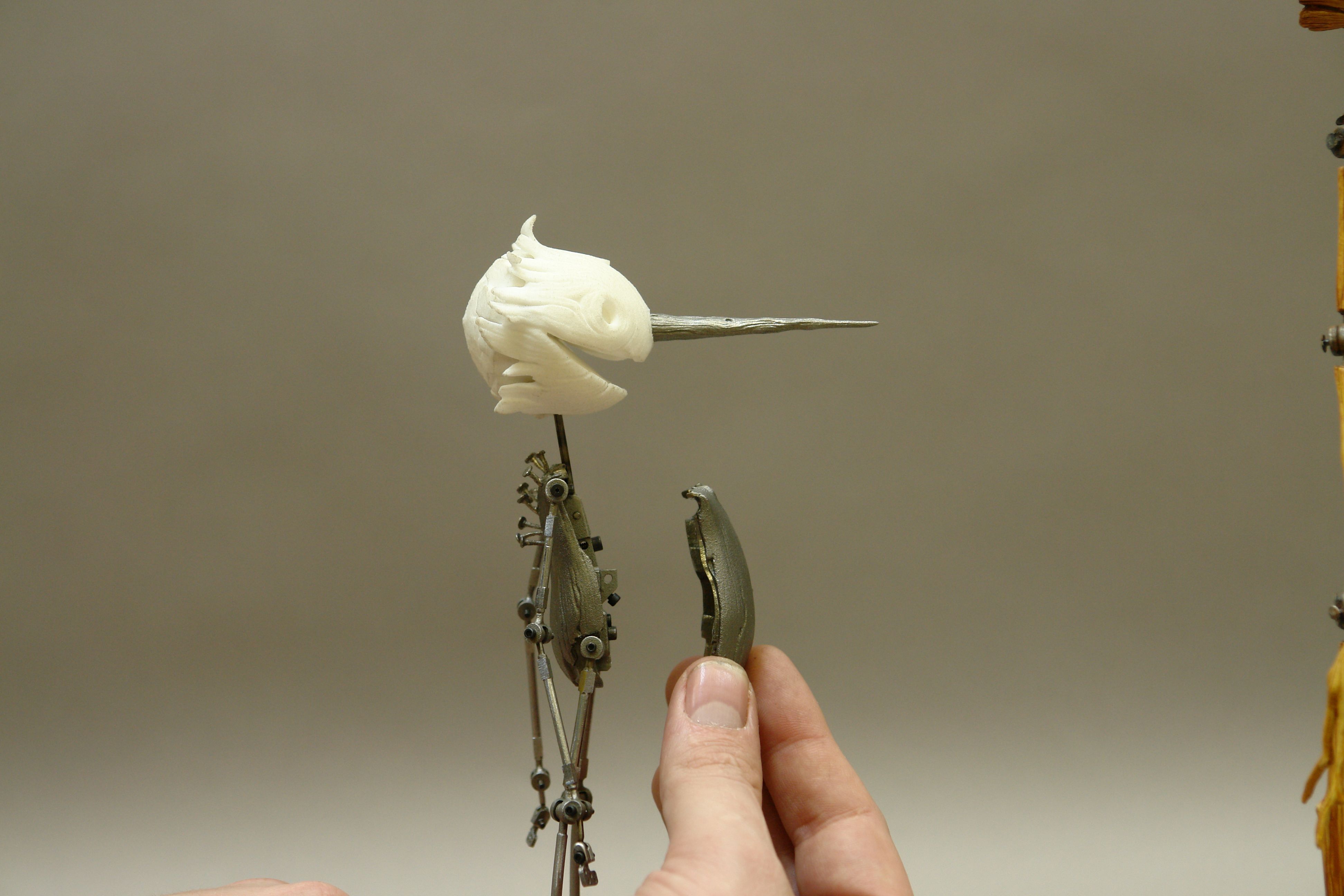
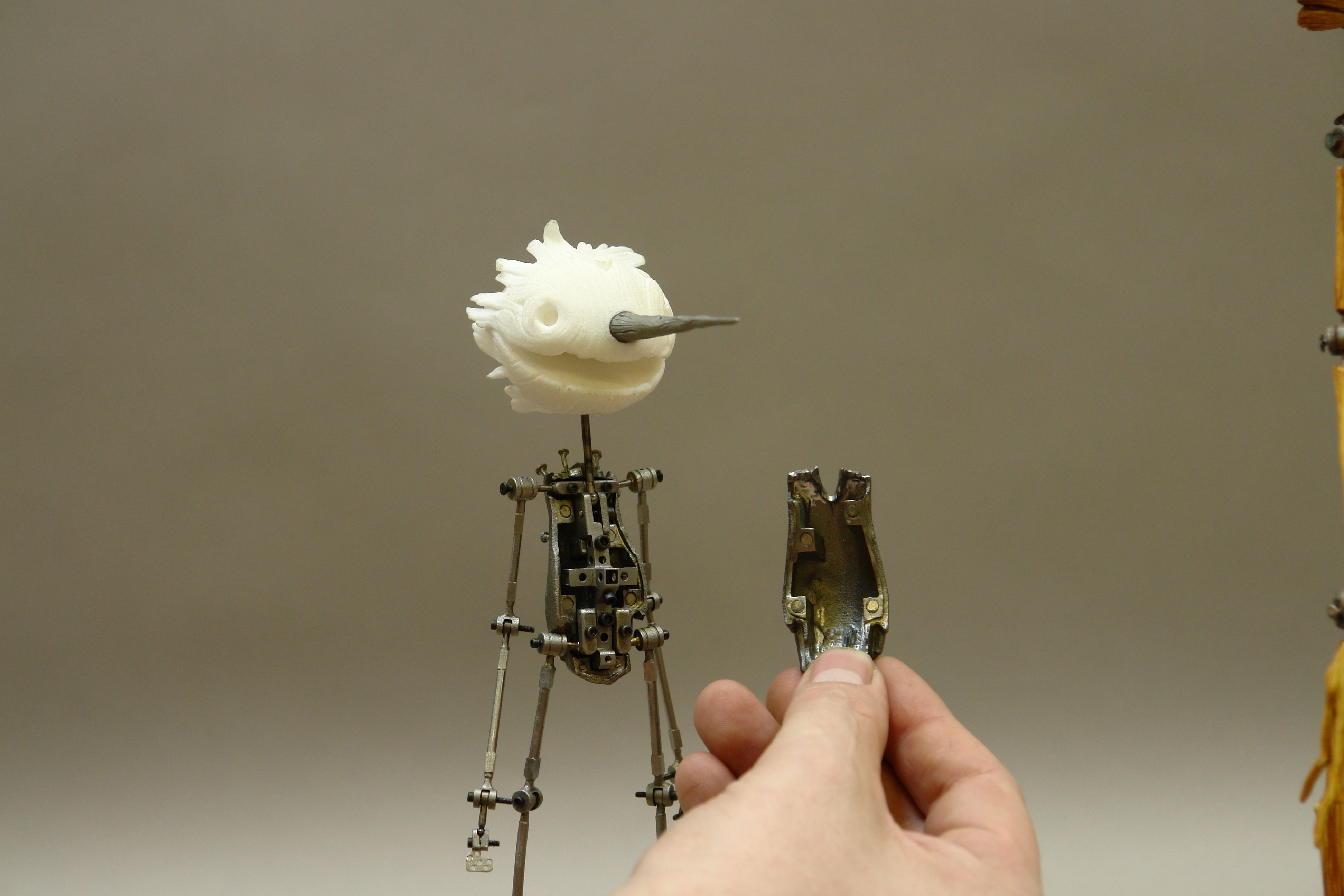
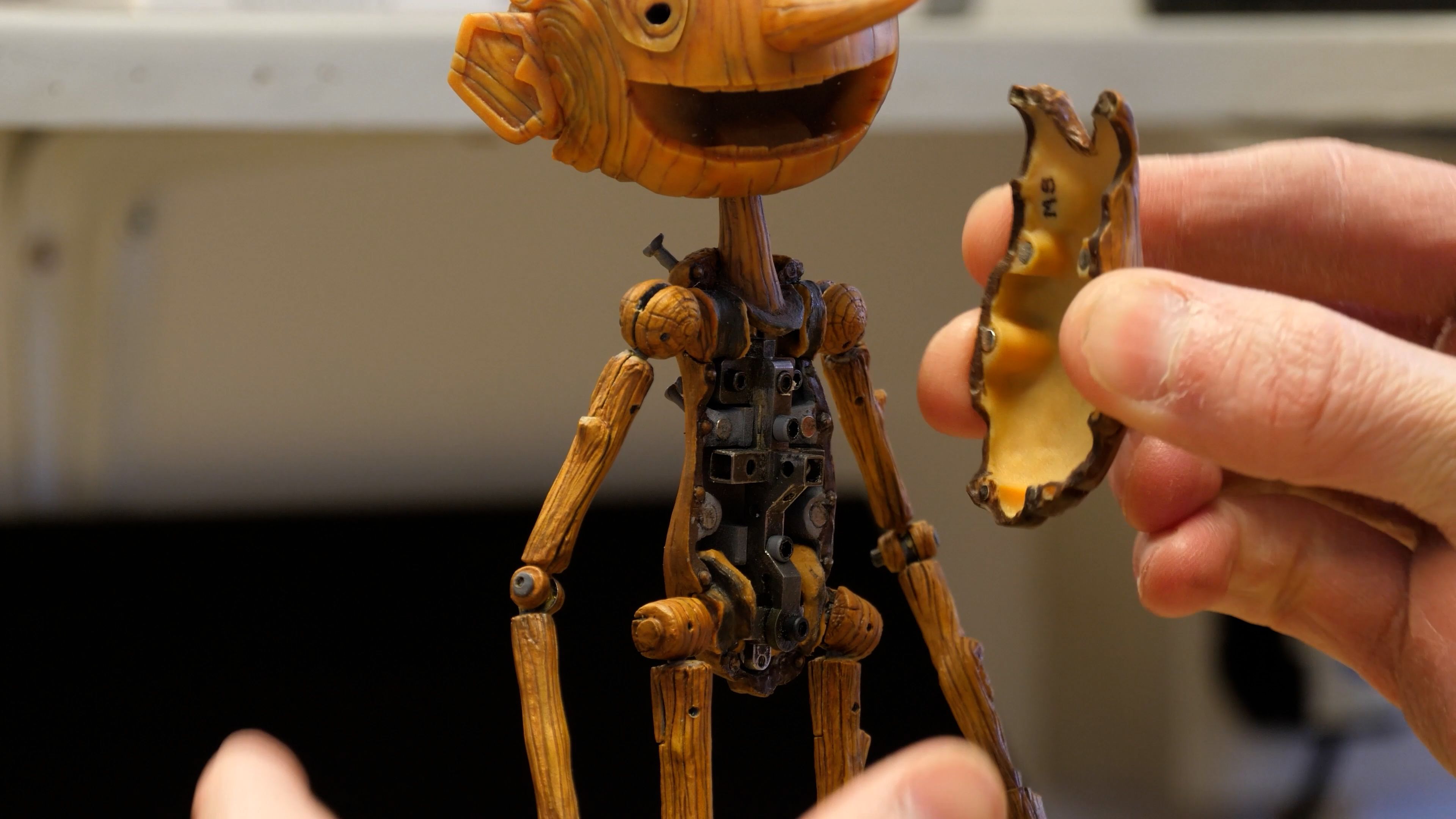
Once the puppets were assembled, a sculptor would apply any organic detailing that was still required, and painters would ensure the printing and paint job matched the preordained colour scheme. Small costume elements – the bandages around Pinocchio’s legs – were also added at this stage.
By the end of the process, the collaborators had landed on a puppet equipped to give a show-stopping performance. In the movie’s plot, he would go on to star centre stage in Count Volpe’s circus, singing, dancing, and provoking the movie’s fascist antagonists, while an animator changed his positioning at 12 frames per second. Thanks to a deconstructed design and magnetised elements, Pinocchio could be moved with ease, and so could his audience.
Around 25 versions of the Pinocchio puppet survived being handled by 40 animators across 1,000 days of production. A bunch of nails hammered into the back of Pinocchio’s head, a design element incorporated to demonstrate Gellepo’s imperfect work, was part of the reason why.
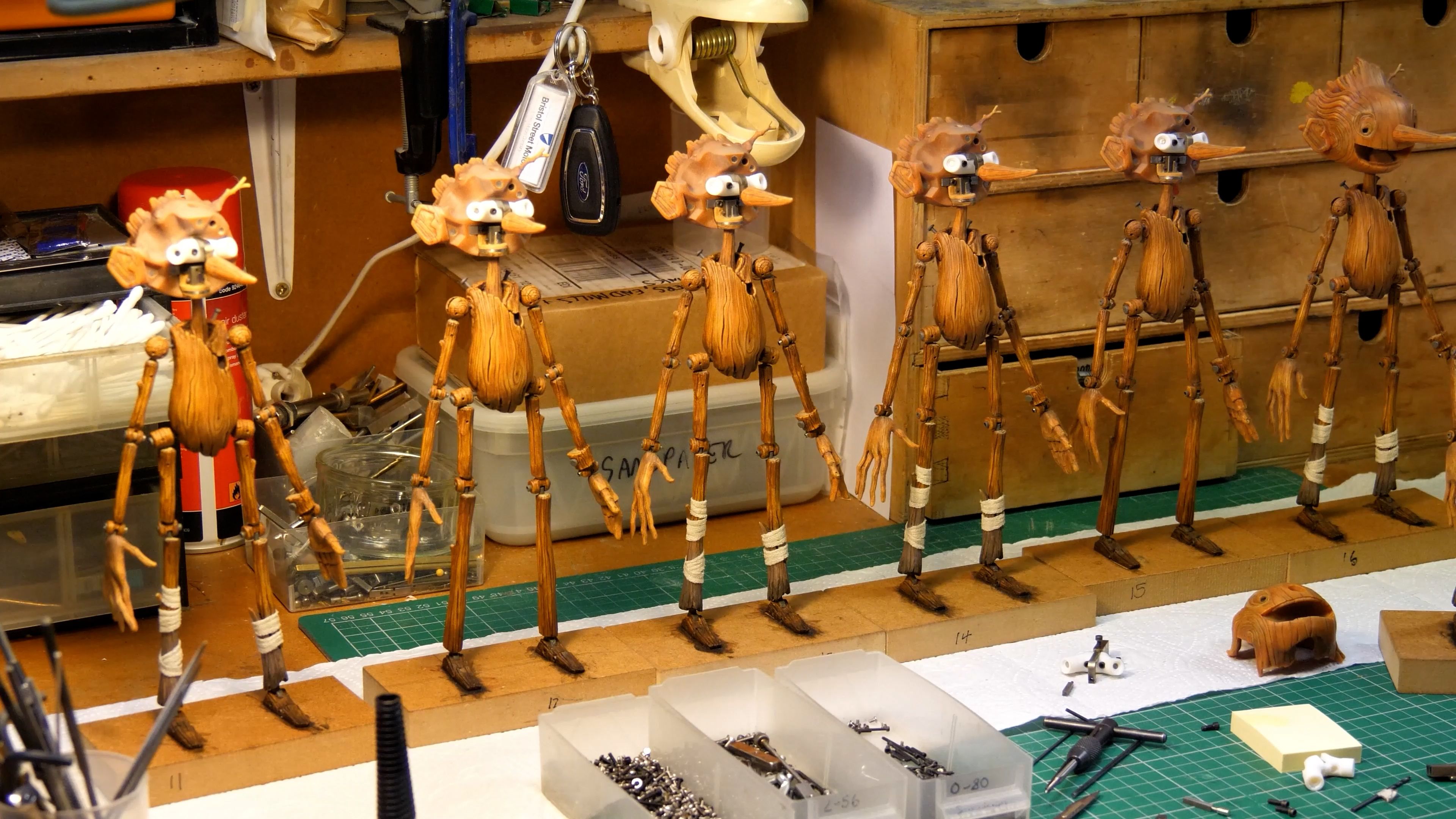
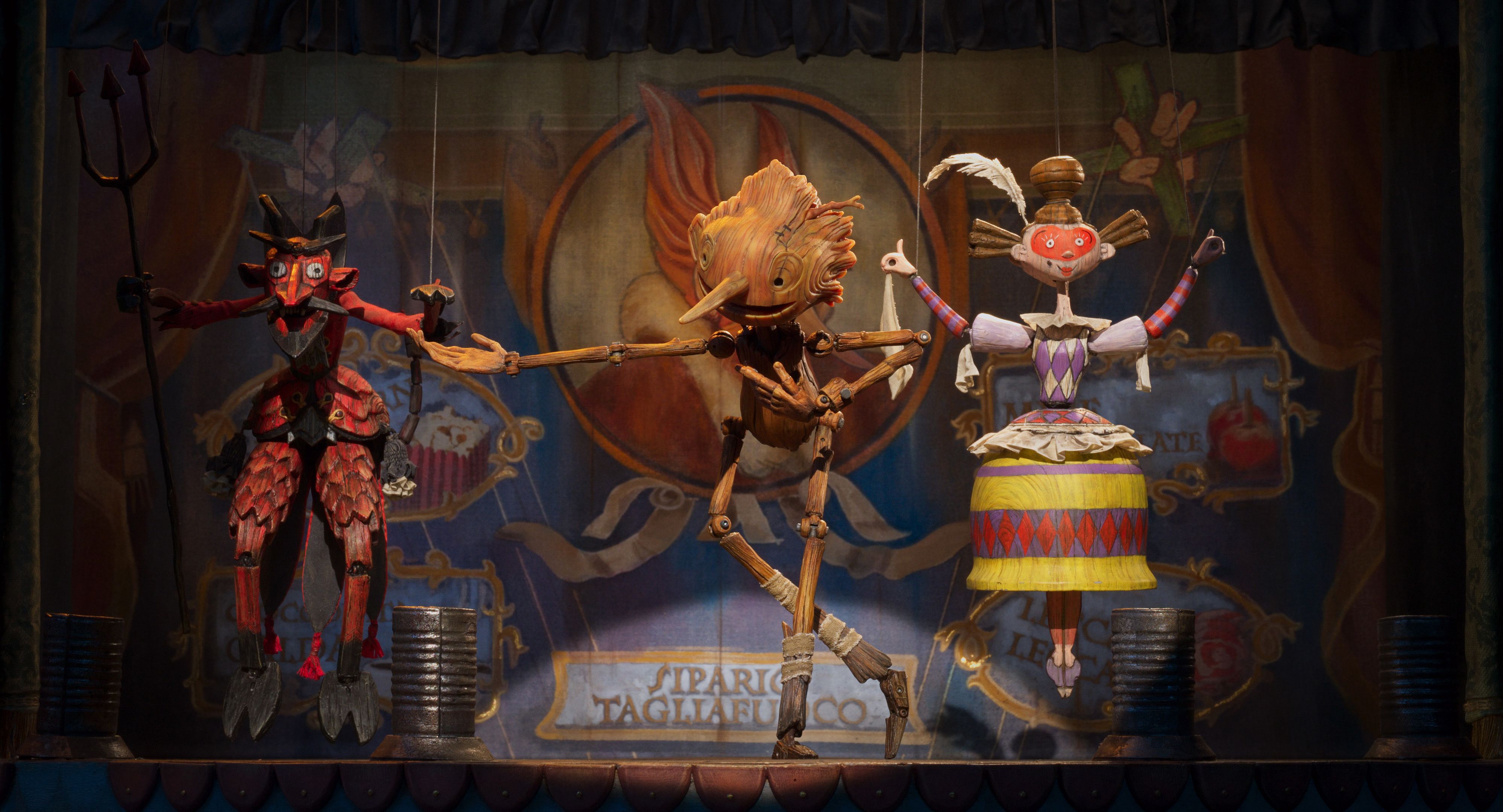
“[Traditionally], there are mechanics going on inside of the torso, and this will be quite a thin shell that will be resin and these nails would be glued on, so they will be prone to breaking,” Pickersgill explains. “To be able to 3D print that torso, have those as part of the shell, I'd challenge you to break it, it made that much of a difference. With the delicacy of the hinges, to cast parts over the top of this, they would have bulked out, and would be more prone to breakage. 3D metal printing allowed us to make a puppet that was much stronger. I don't think we could have done that with a traditionally made puppet.”
Similarly, FATHOM had designed the facial elements with enough wall thickness to ensure the head wouldn’t degrade and the puppet could withstand a three-year production cycle. This resilience, teamed with the full-colour aesthetics and dynamic design of Pinocchio, has facilitated a movie that has so far generated 108 million USD in income.
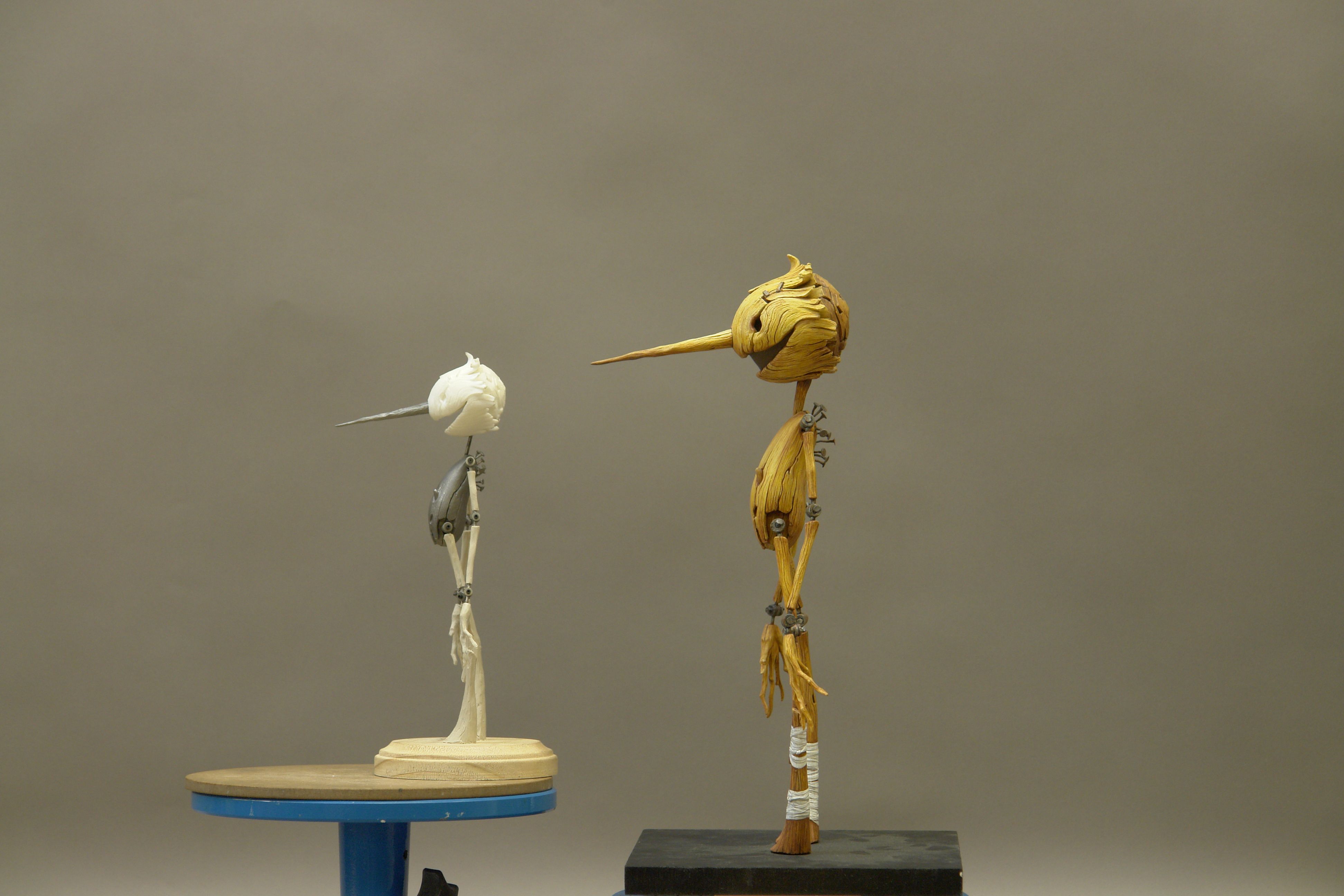

A story so often told, yet this modern approach to the manufacture of its main character has still captured the imagination.
“The animators, particularly with Pinocchio, they've been very complimentary about working with that particular character,” Mackinnon says. “The ease that they found working with that character and what they get out of it. Pinocchio is in every scene and so it's a very energetic performance. They've put that puppet through the mill, and they hardly broke, which is unusual, but all that engineering and all the skill and the thought process was a big part of that.”
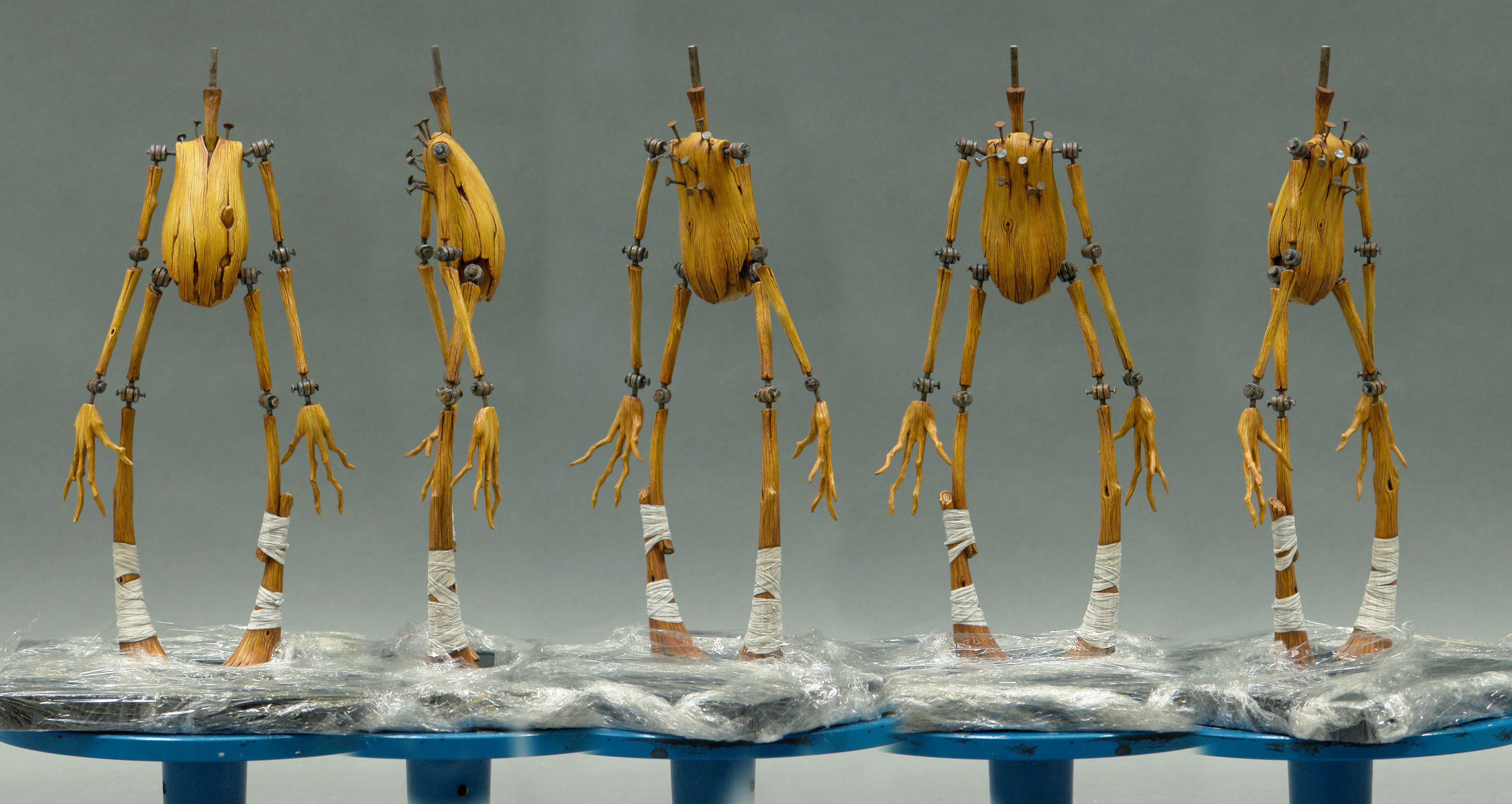